Leak detection is a crucial method for ensuring the sealing and safety of equipment, especially in industrial applications that require high precision. Helium leak detection technology has become the preferred testing method in many high-demand environments due to its high sensitivity and ease of detection. Traditional leak testing methods use gases like nitrogen or air, but helium, with its unique molecular characteristics and low background concentration, shows significant advantages in detecting small leaks. This study will explore the application advantages of helium in leak testing and analyze its practical effects in various industries.
1. Physical and Chemical Properties of Helium
Helium (He) is an inert gas with highly stable chemical properties, making it unlikely to react with other substances. It is non-toxic and non-corrosive. Helium’s physical properties, especially its small molecular weight and low viscosity, give it excellent permeability. Compared to other gases, helium’s small molecular size allows it to permeate through tiny pores more easily, thereby enhancing the sensitivity of leak detection.
In addition, the natural concentration of helium in the atmosphere is extremely low, meaning its leak rate can be detected sensitively by detectors. During helium detection, background gas interference is minimal, further improving the accuracy and reliability of the detection.
2. Principles of Helium Leak Testing
The basic principle of detección de fugas de helio is to allow helium to penetrate through small leaks in equipment or containers and capture the concentration change of the leaking gas using specialized detectors. Common detection methods include:
2.1 Mass Spectrometry: This method uses a mass spectrometer to detect changes in the mass and concentration of helium, enabling precise identification of the leak location and rate.
2.2 Gas Detection Method: This method involves injecting helium into the equipment and monitoring the concentration change with external detectors to further determine if a leak has occurred.
Both methods provide highly sensitive and fast leak detection results, suitable for accurate measurement of small leaks.
3. Advantages of Helium Leak Testing
3.1 High Permeability
Helium’s very small molecular weight allows it to permeate through almost all common materials’ small pores. This characteristic makes helium more effective than many traditional gases when detecting small leaks.
3.2 High Sensitivity
The concentration of helium in the Earth’s atmosphere is extremely low, approximately 5.2 × 10^-6, meaning there is less interference from environmental gases when it leaks. This feature allows helium detection instruments to more accurately identify minute leaks.
3.3 Safety
Helium is an inert gas and does not react with other chemicals, making it non-toxic and harmless. This makes it widely used in environments with high safety requirements, such as aerospace, electronics manufacturing, and pharmaceuticals.
3.4 Ease of Detection
Helium can be easily detected using mass spectrometry, helium detectors, and other equipment. Modern helium leak detection instruments have high detection precision and fast response speed, allowing real-time monitoring of gas leak concentration and rapid identification of leak points.
4. Application Areas of Helium Leak Testing
4.1 Aerospace
In aerospace, helium leak detection is widely used to inspect fuel systems, pressure vessels, and spacecraft sealing systems. Given the high sealing requirements of spacecraft, any minor leak could lead to equipment failure or safety hazards. Helium detection ensures the integrity and safety of the equipment.
4.2 Electronics Manufacturing
In the production of electronic components, especially in the manufacture of integrated circuits (ICs), helium leak testing is used to check the sealing of packages. This process requires high-precision testing to prevent gas leaks or contaminants from entering the components, which could affect their performance.
4.3 Pharmaceutical Industry
The pharmaceutical industry has stringent requirements for clean environments and equipment sealing, particularly in sterile production processes. Helium leak testing ensures the integrity of equipment seals and the reliability of sterile environments, preventing contamination of medicines.
4.4 Oil and Gas
In oil and gas exploration and production, helium leak detection is used to check the sealing of pipelines and storage tanks, ensuring the safety and stability of the transport system.
5. Limitations and Challenges of Helium Leak Testing
Although helium leak detection has many advantages, it also has certain limitations. For example, the equipment required for helium detection can be expensive, and the process requires specialized instruments and trained personnel. In some cases, helium leak detection may be affected by environmental factors, such as temperature and humidity, which can influence the detection results. Therefore, comprehensive factors must be considered when selecting the appropriate detection method for practical applications.
6. Conclusion
Helium leak detection, with its high sensitivity, permeability, safety, and ease of detection, has become the preferred gas for detecting small leaks in various industrial fields. Although there are some limitations, with advancements in technology, helium leak detection methods and equipment have become more precise and economical. It is expected that helium leak detection will be applied in more fields in the future. By continuously optimizing helium leak detection technologies, industrial production safety and reliability can be further improved.


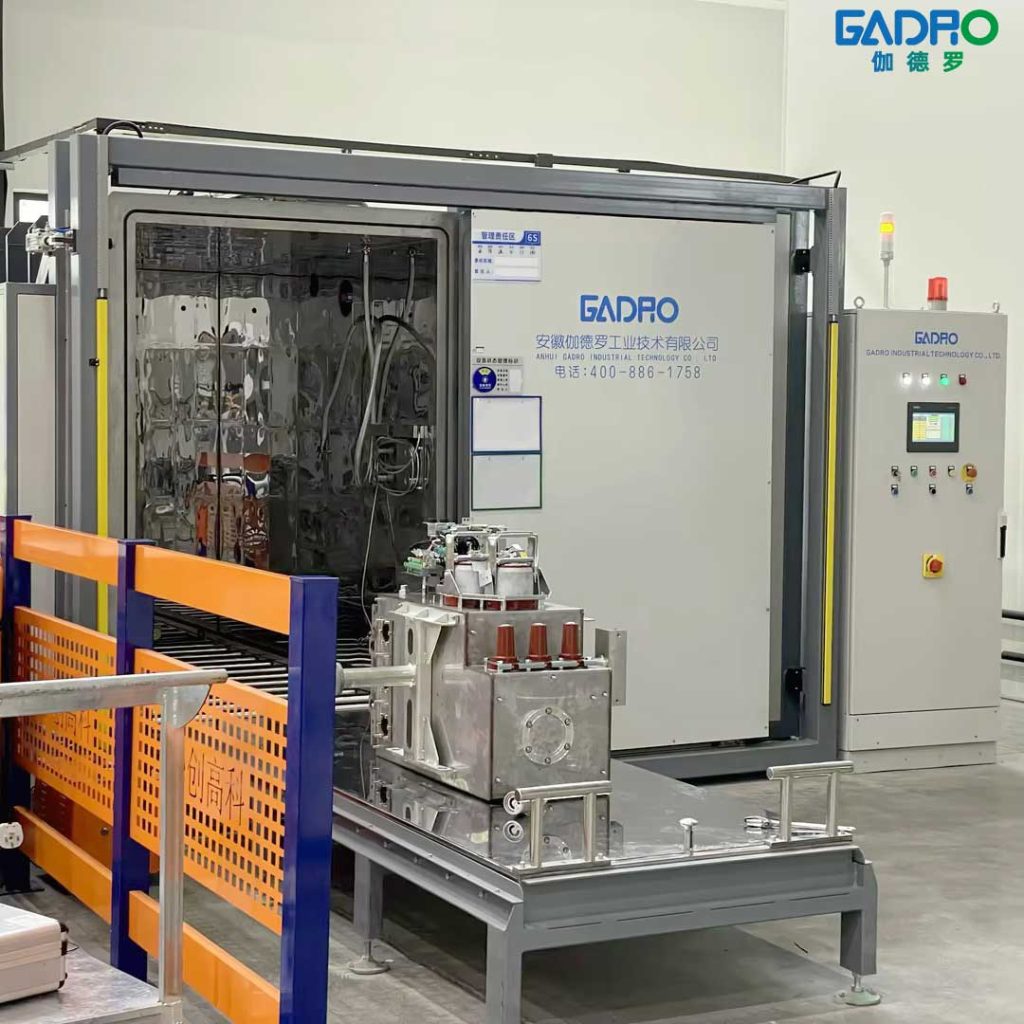