Los distintos tipos de fugas se comportan de forma diferente. La geometría de la fuga, la presión, el material, la humedad, la temperatura y el caudal son factores que influyen en el comportamiento de una fuga. Demasiados factores que interfieren plantean grandes desafíos a la detección de fugas.
Los siguientes tres tipos difíciles de detectar son ejemplos que he recopilado y analizado.
Tipo 1: Fugas en el haz
Al utilizar gas trazador para detectar fugas, a veces es posible que solo se pueda localizar una zona estrecha. Al mismo tiempo, se obtiene una indicación de fuga, pero está muy lejos del objeto de prueba (unos pocos pies/decímetros), por lo que se desconoce la causa.
La fuga que encuentre puede ser un haz muy pequeño y de alta velocidad de gas trazador, casi como un haz de láser estrecho. Cuanto más lejos esté de la fuga, más se extenderá el haz, pero incluso a una distancia considerable de la fuga, el haz puede seguir siendo muy estrecho.
El haz de gas puede impactar al operador o las estructuras circundantes y “rebotar”, lo que hace que el operador pierda de vista de dónde proviene realmente el haz. Detectar esta fuga difícil de detectar puede ahorrar un tiempo valioso de inspección.
Tipo 2: Fugas en piezas de fundición de aluminio
Las piezas fundidas de aluminio pueden contener bolsas de aire que se forman como resultado del gas atrapado en el metal fundido a medida que se solidifica. Estos poros pueden ser muy grandes y evidentes, o pueden ser muy pequeños y causar pocos problemas.
Los poros pueden estar encerrados dentro de la pieza, sin aberturas para conectar las superficies, pero también pueden conectar una o ambas superficies. El último caso creará una vía de fuga a través de la fundición de aluminio.
Las fugas en la fundición pueden tener forma de orificios, que a su vez pueden actuar como un tubo delgado a través de la fundición. Estas fugas son en gran medida predecibles. Sin embargo, las fugas también pueden ser porosas, lo que generalmente implica una gran cantidad de fugas muy pequeñas que juntas pueden crear una fuga más grande. Si el área de la fuga se vuelve grande, puede ser difícil detectar la fuga con una pistola de succión porque la pistola no puede detectar el flujo de fuga general.
Una forma de fuga difícil de detectar en las piezas fundidas de metal es la filtración, que se conecta a una cavidad oculta más grande que actúa como depósito de gas durante la prueba de fugas.
Esta estructura puede provocar un retraso considerable entre el proceso de inyección de gas y el proceso de fuga de gas hacia el lado opuesto del punto de fuga.
En cuanto a las fugas semiocultas, totalmente cerradas, también son difíciles de detectar si la prueba de fugas se realiza en una pieza “tal como está fundida” y si la prueba de fugas va seguida de algún tipo de mecanizado que abre dichos orificios de fuga cerrados.
Los pequeños orificios de aire también se pueden sellar durante diversos tratamientos con líquidos o procesos de pulverización. Esta situación debe considerarse cuidadosamente al decidir en qué parte del proceso de fabricación se debe realizar la detección de fugas.
Por lo general, se recomienda la detección de fugas después de completar los procesos de mecanizado y decapado y antes de realizar tratamientos de superficie como pintura, recubrimiento electroquímico u oxidación.
Tipo 3: Fuga discreta de líquido
Cuando se prueba un producto para detectar fugas de líquido, el resultado puede ser que el producto no tenga fugas, pero las fugas se pueden detectar si se inspecciona el producto con un método de detección de fugas de gas trazador.
Los orificios de fuga pueden hacer que el líquido que se está filtrando llegue a la superficie de la fuga a una velocidad tan lenta que el líquido se vaporiza al llegar a la superficie exterior del objeto. El líquido se evapora tan rápido que no queda rastro visible de la fuga en el punto de fuga.
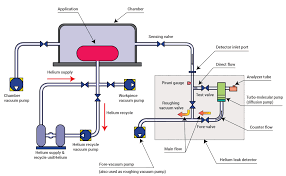